Back
Parameter
Items |
Parameter |
Material Thickness |
0.3-0.6mm |
Material Thickness |
0.3-0.6mm |
Forming Steps |
20steps |
RollerMaterial |
45# steel, coated withChrome |
Driving Motor |
11KW |
Hydraulic Cutting Power |
4KW |
Shaft Diameter |
75mm |
Hydraulic Pressure |
10-12MPa |
Power Supply |
380V/50HZ/3Ph (can be specified by user) |
Cutting Type |
Hydraulic cutting, stop to cut |
Tolerance |
±1.5mm |
MaterialofCutting Tool |
Cr12 |
Control System |
PLC with touch screen |
Machine Dimension |
10800*1350*1650mm |
Machine Net Weight |
5.5Tons |
Metal Sheet Sample Pictures
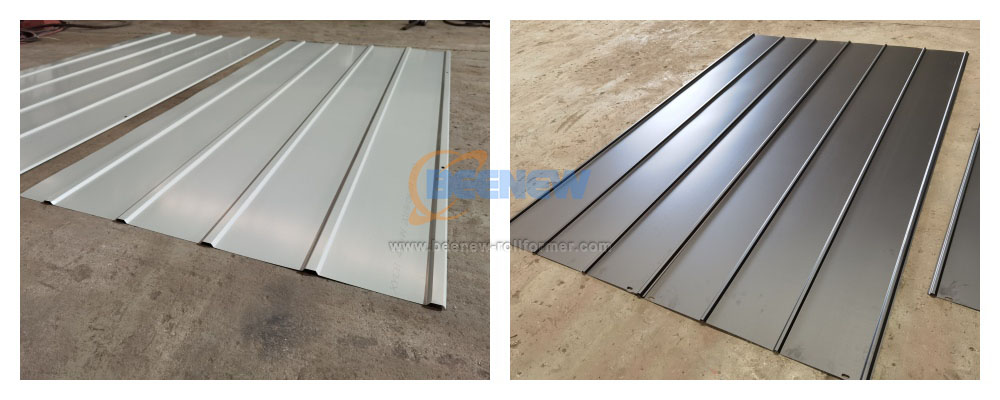
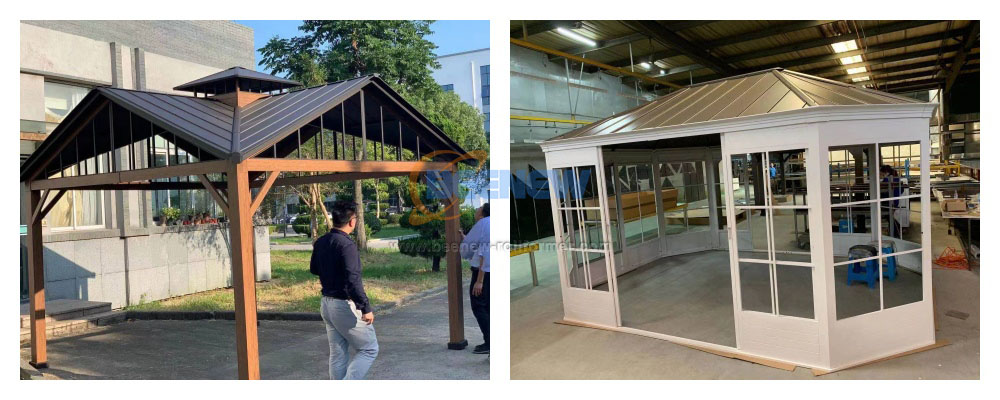
The metal roll forming equipment from Beenew Machinery is engineered to produce high-quality roof panels with advanced technology and efficient performance. It supports a wide range of materials, including Alu-zinc, with a thickness range of 0.35mm to 0.8mm. The effective width is 1020mm, and the feeding width is approximately 1220mm, ensuring robust production capabilities. The system accommodates material yield strengths between 235-550MPa, offering excellent durability for roofing applications.
Hydraulic Decoiler
The metal roll forming equipment is equipped with a 5 Ton*1250mm hydraulic decoiler, designed for smooth and efficient coil feeding. The hydraulic coil inner hole expanding system is driven by a 3KW pump motor, providing easy handling and size adjustments. The taper wedge expanding system ensures stability with a load capacity of up to 5 tons. It supports coils with an inner diameter of 510±30mm, an outer diameter of up to 1300mm, and a maximum coil width of 1250mm.
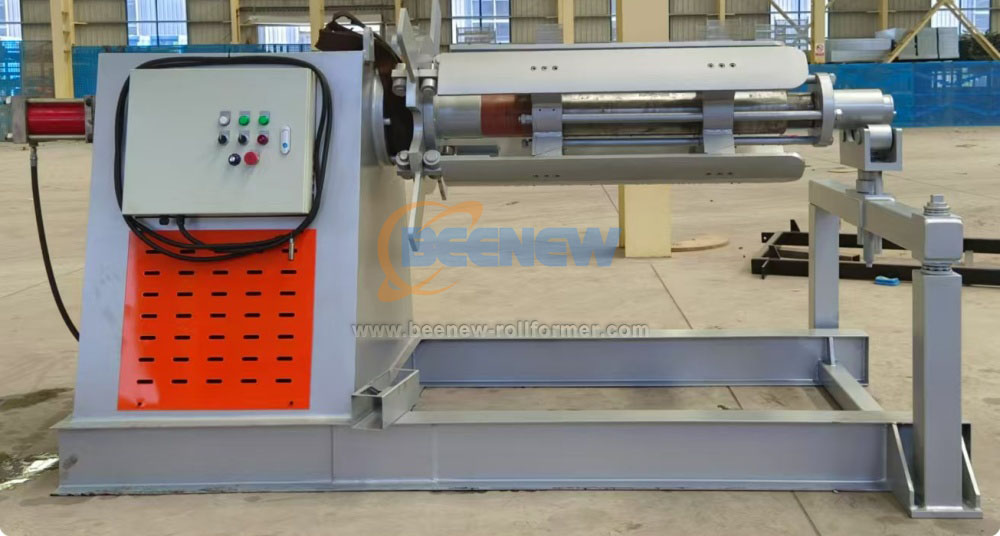
Feeding Guide & Manual Pre-shearing Device
This metal roll forming equipment includes feeding guide that manage working thicknesses up to 0.6mm. The manual pre-shearing device features smart cut control that trims only the end of the final sheet, minimizing material waste and ensuring precise cuts.
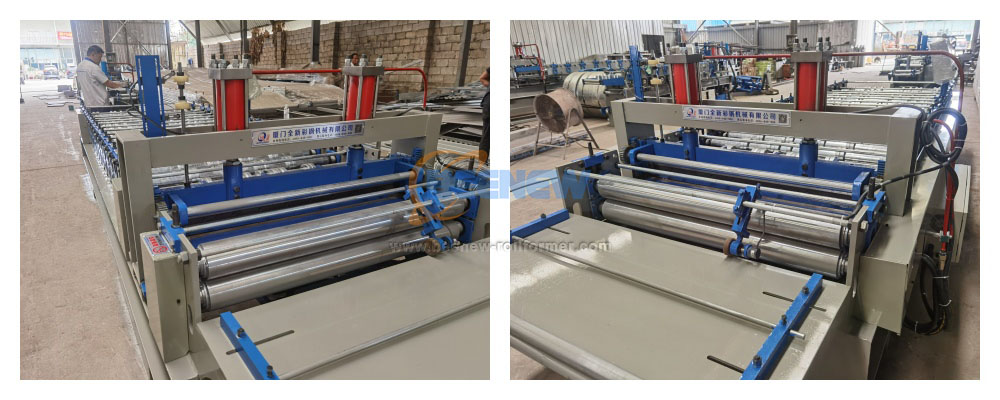
Main Roll Forming Machine
The machine's main section operates through a gear/sprocket driving system, ensuring stable and efficient functioning. The metal roll forming equipment has 18 forming stations made from 45# steel, processed on CNC lathes, and coated with hard chrome for durability. The shaft diameter is Φ75mm, contributing to reliable operation. The main motor is rated at 11KW, and the line runs at approximately 20m/min.
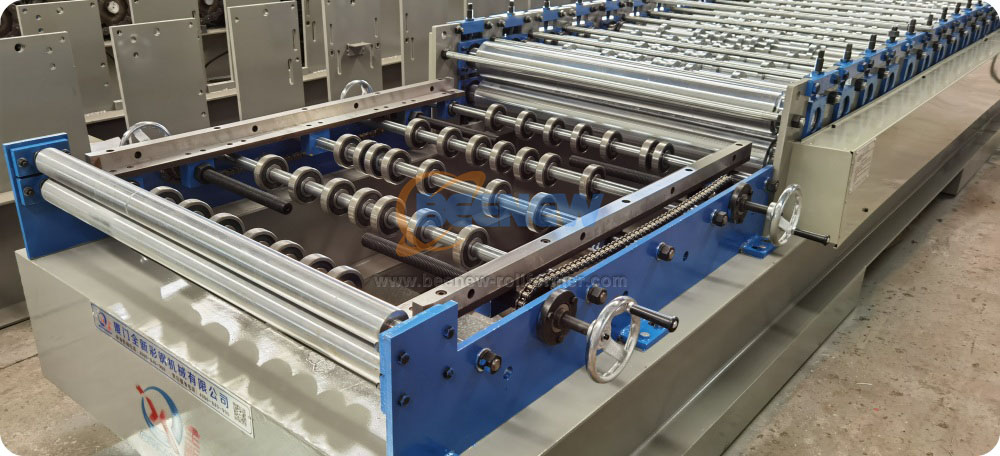