Back
Alternative sources of energy
BIOFLUID - biomass gasification Environmental sound energy
Biomass and RDF (refuse derived fuel) gasification plant.
Gasification of raw material undergoes in presence of the air in the fluidized-bed gasifying generator at temperature 850 - 900°C. Tar-containing residues that resulted from raw material pyrolysis are eliminated through thermal cracking in the gasifier and then they are cleaned by washing in cool water. Heat generated from cooling gas in the heat exchangers is usable for the purposes of drying sawn wood, heating housings, and or for drying of the raw material entered therein. After cooling, the energy-gas is burned in the co-generation plant with combined power and heat production.
Another possibility of applying the energy-gas is a replacement of conventional sorts of fuels (natural gas, LPG, fuel oil, etc.) for operation of lime-kilns, brickplants, ceramic plants, annealing ovens, and elsewhere the above fuels are burned up. When used in such applications, it is not necessary to cool the energygas, its dedusting is ensured with cyclone separator. Residual tar substances go with gas to direct burning.
Process total efficiency |
81 % |
Low heat value |
5 - 7 MJ/Nm3 |
Power & output of the plant with co-generated production of electricity and heat
Electricity output (kw) |
250 |
500 |
750 |
1000 |
Heat output (kw) |
550 |
1100 |
1650 |
2200 |
Biodiesel production form rape-seed - replacement for classic fuels
A complete technological plant including the rape seed receiver up to the storage and spedition of biodiesel.
Fully automatized batch process of bio diesel production is applied using a minimum quantity of chemical substances, being of remarkable simplicity in terms of maintenance and operation.
Oil pressed out at cool conditions from the rape seed, undergoes further physical and chemical processing at normal temperature and actually atmospheric pressure with chemical action of methanol, cifric acid and potash lye onto the methyl ester rape seed fatty acids (biodiesel).
The methyl ester is modified, by washing out with water and stripping at temperature 80 °C to gain the product that is in compliance with the fuel standards for compression ingnition engines. The high quality of the product is the main advantage of this process.
Reesterification unit for biodiesel productivity plant with capacity 2100b/y available
Production capacity
Reesterification is designed for the daily production capacity of 2, 4, 6 and 10 tons. The annual production capacity depends on amount of operating days in the year. According to the customer´s option, the present plant can be delivered also for smaller or bigger production capacity. In this case the oil press - shop machinery, where the change in output makes the most substantial difference in price is optimized in its capacity design upon what is required.
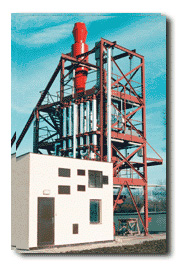